
Robert Kunzmann GmbH & Co. KG

How the Kunzmann Group Now Gains the Equivalent of 4 FTEs with aspaara
A digital process simulation gives Robert Kunzmann GmbH & Co. KG the leeway of four additional full-time equivalents and shortens workshop throughput times by three days—an unmistakable productivity boost for the ten Mercedes-Benz locations in the Rhein-Main-Spessart region.
+4FTE
More Full-Time Equivalents in Capacity Utilization
-3 Days
Shorter Throughput Time (key-to-key time)
The Customer: Robert Kunzmann GmbH & Co. KG
The Kunzmann Group is one of Germany’s largest Mercedes-Benz dealer organizations. With ten locations and over 1,000 employees in the Rhein-Main-Spessart region, this family business—founded in 1935—serves customers of Mercedes-Benz, smart, and FUSO in sales, service, and parts logistics. State-of-the-art workshop technology, a broad vehicle lineup, and a strong commitment to training around 180 apprentices each year ensure Kunzmann’s long-term service quality and sustainable success.
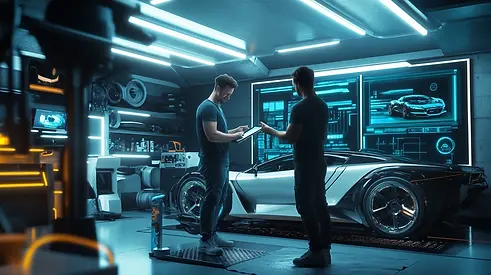
Challenge
-
Processes are constantly interrupted, and changeovers cost efficiency.
-
Coordinating the delivery of vehicles from branch locations and their handover for repairs in Aschaffenburg is logistically very complex in order to achieve an efficient workflow.
-
It is effectively impossible to determine the future capacity of each department.

Solution
-
Within two weeks, a Bodyshop Planning Assessment (BPA) was conducted with experts from both sides.
-
The digital twin for the Aschaffenburg location was calibrated in aspaara® and the potential was simulated.
-
The optimization strategy “Push to the Left” was applied to measure its effect on the KPIs.
-
A detailed project plan for the pilot launch was developed, including both internal and external resources.